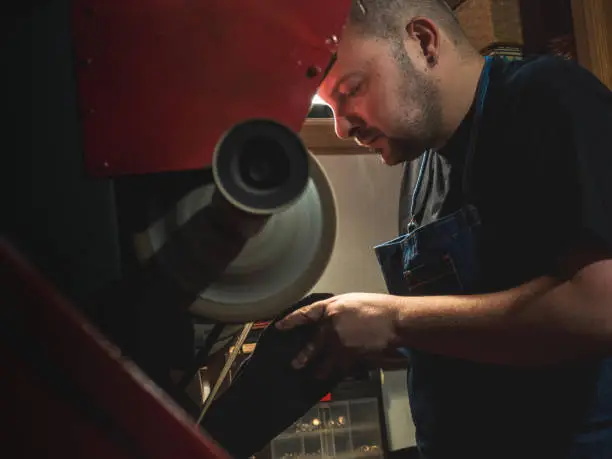
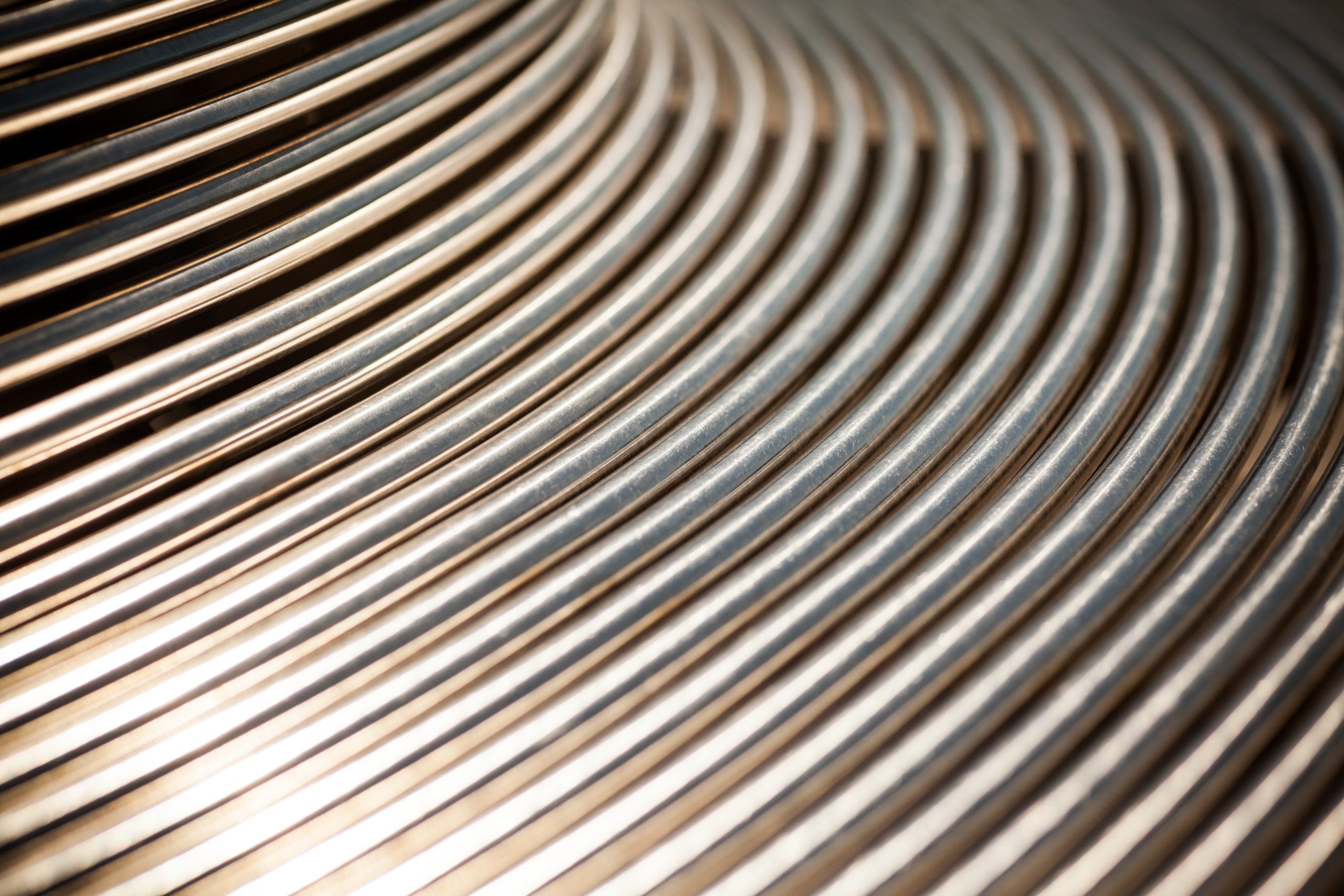
A Step-by-Step Guide to Custom Metal Spinning
Metal spinning is the versatile and precise method of shaping metal into axially symmetrical forms. Using just a flat metal disc and a rotating mandrel, it’s possible to create everything from shallow pans to deep cylindrical housings, conical forms, and much more. Metal spinning is particularly appealing because it can produce seamless parts with excellent structural integrity—often with minimal material waste.
In this blog, we walk through the complete step-by-step process of custom metal spinning, explaining each stage, from preparing the raw material to the finishing touches that complete the component.
1. Choosing the Right Material
Material selection is crucial in metal spinning. Common choices include aluminium, stainless steel, copper, brass, and even titanium. Each metal has its own advantages and forming characteristics, which help determine the best fit for the specific use case.
Aluminium, for instance, is lightweight and highly malleable—ideal for intricate shapes or where corrosion resistance is a factor. Stainless steel offers greater strength and durability but requires more force to spin. The right choice depends on the intended use, its required strength, and its desired appearance.
2. From Design Brief to Blank Preparation
Every metal spinning project requires a detailed design. Engineers start by defining the part’s geometry, the preferred material, and any critical tolerances or finishing requirements. This design creates the physical starting point of a spinning project: a flat metal disc known as a blank.
The blank is cut to a size that matches the dimensions and depth of the final part. Accurate cutting at this stage is essential, as it influences everything that follows—from material efficiency to forming time and final tolerances.
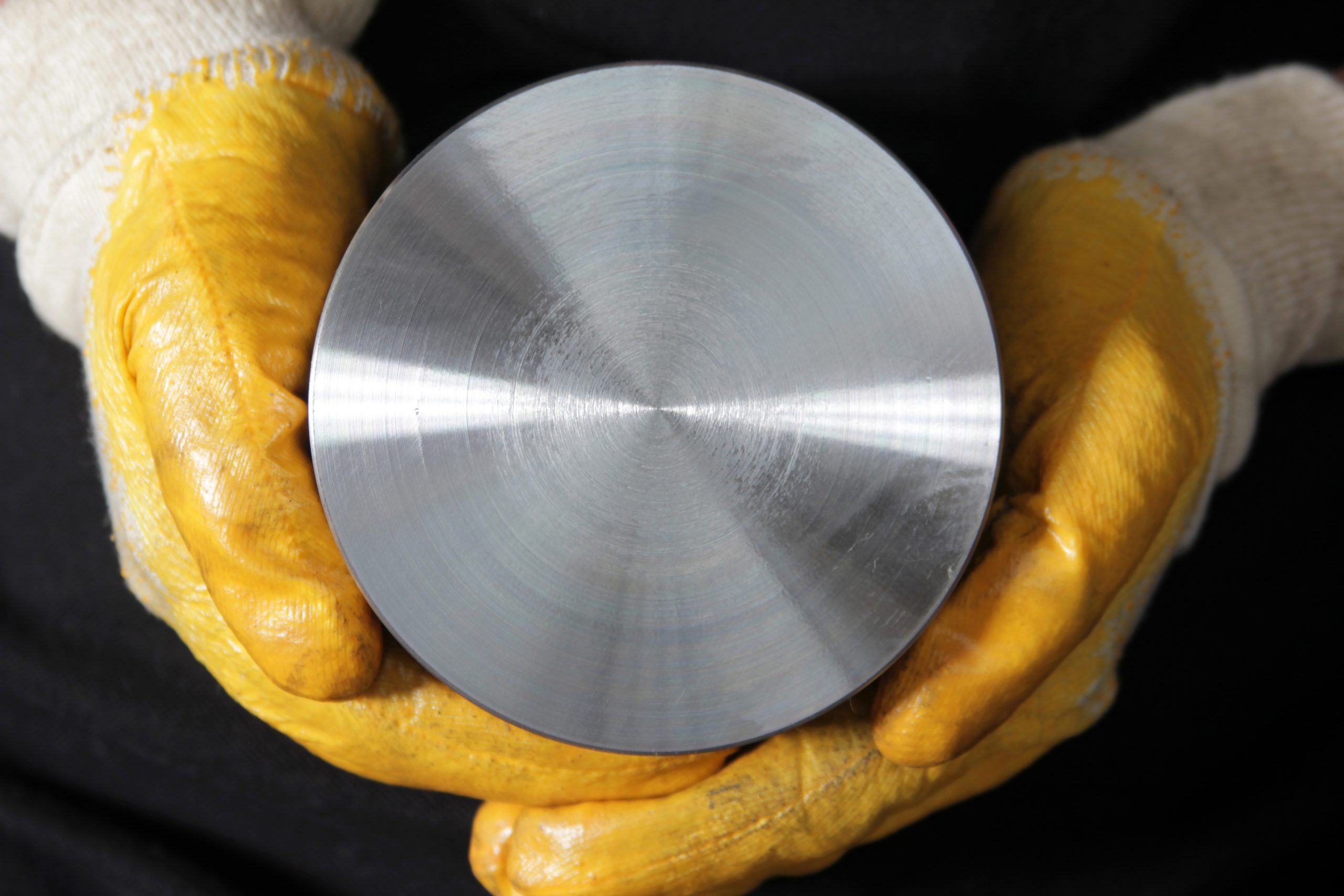
3. Mounting the Blank and Setting Up the Lathe
The blank is mounted onto a spinning lathe, held firmly in place against a mandrel. The mandrel is a form—usually made from steel or aluminium—that defines the interior shape of the finished part. It is mounted to the lathe’s headstock, with the blank clamped between it and a pressure plate or follower block at the tailstock end.
Proper alignment at this stage is vital. If the blank is even slightly off-centre, the spinning process can introduce defects, uneven wall thicknesses, or worse—complete failure.
4. The Spinning Process Begins
With the blank secured and the lathe rotating, a forming tool is brought into contact with the surface of the metal. This tool applies pressure to gradually push the blank over the mandrel. Traditionally, the forming tool was guided by hand, but now, Computer Numerical Control (CNC) often controls this process digitally.
This shaping process typically takes place over several passes. Each pass moves the metal closer to the shape of the mandrel. The skill lies in knowing how much pressure to apply, where to apply it, and when to ease off. Applying too much force can cause the material to wrinkle or tear. Applying too little will prevent it from forming completely.
As the metal spins, it work-hardens. In some cases, especially with tougher materials or deep draws, it may become necessary to pause and anneal the component—heating it and allowing it to cool slowly—to restore ductility before continuing.
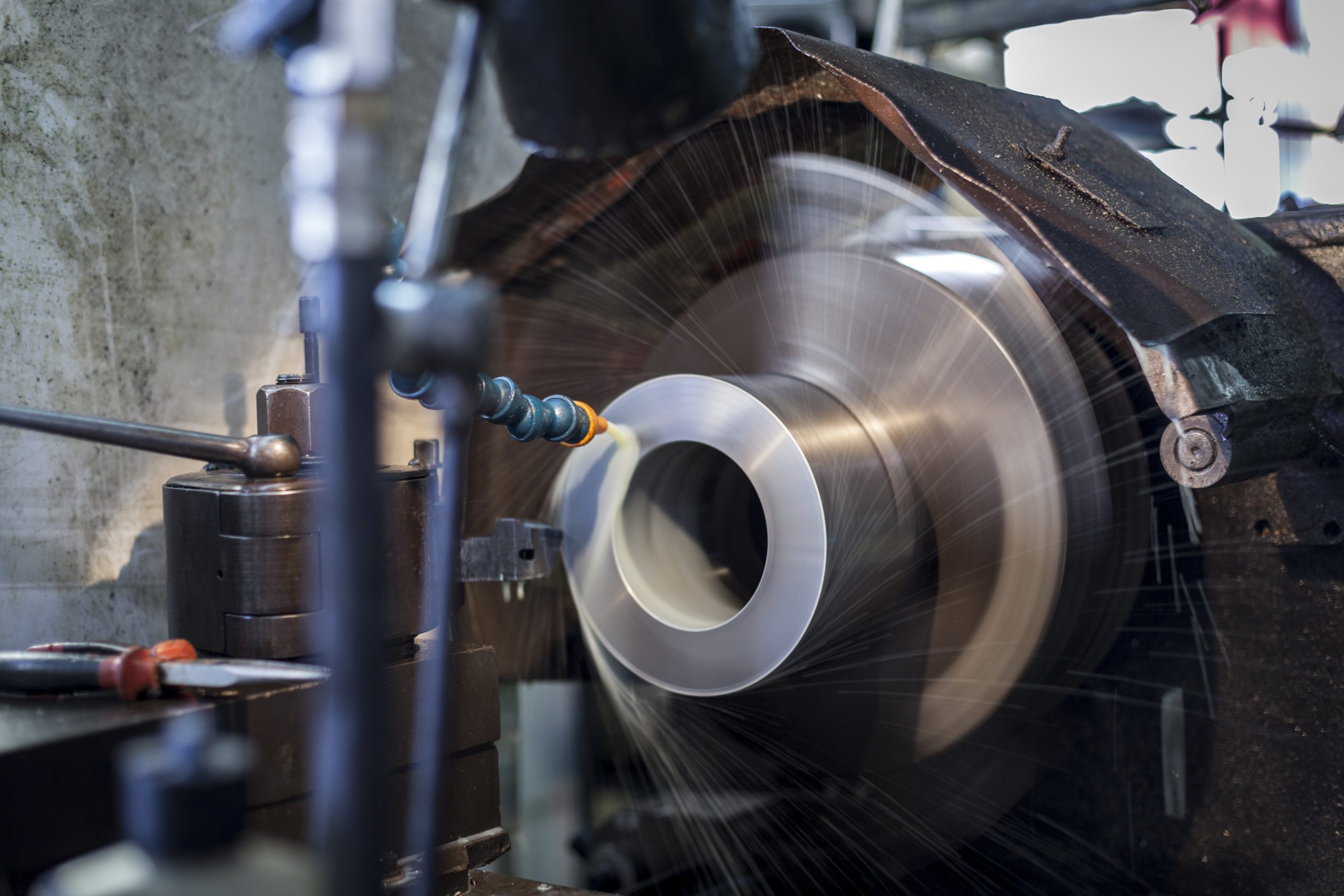
5. Feathering, Finishing and Planishing
With the rough form created, we use feathering strokes to remove any ripples or wrinkles from the surface. These are lighter, sweeping passes with diminishing pressure, intended to smooth the surface without thinning the wall too much.
At this point, the metal is fully conformed to the mandrel, and the shape is set. We may use a final planishing pass to refine the surface—flattening any minor imperfections and bringing the part to a uniform finish.
6. Trimming and Edge Treatments
Next comes trimming. This step removes any excess material around the rim of the fabricated part using a sharp trimming tool. The goal is a clean, even edge that matches the design specifications precisely.
Depending on the application, the edge may also be further treated—for example, beaded for strength, curled for safety, or flanged to allow mating with another component.
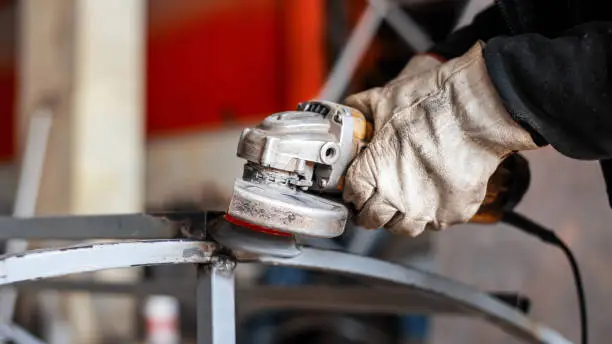
7. Quality Checks and Removal
Once complete, we remove the spun part from the lathe. In most cases, this involves loosening the tailstock and sliding the part off the mandrel. Occasionally, vacuum or thermal locking can occur—especially with deep parts or reverse tapers—in which case we may need additional steps such as creating vent holes or gentle material heating.
After removal, the part undergoes inspection to check for surface quality, dimensional accuracy, and any signs of deformation.
8. Optional Post-Spinning Processes
Metal spinning can produce parts with excellent finish straight off the lathe, but further processing may be required for specific applications. This processing might include decorative polishing, painting, plating, or machining to add features such as holes, threads, or flanges. The result is a component that’s not only structurally sound but also functionally ready.
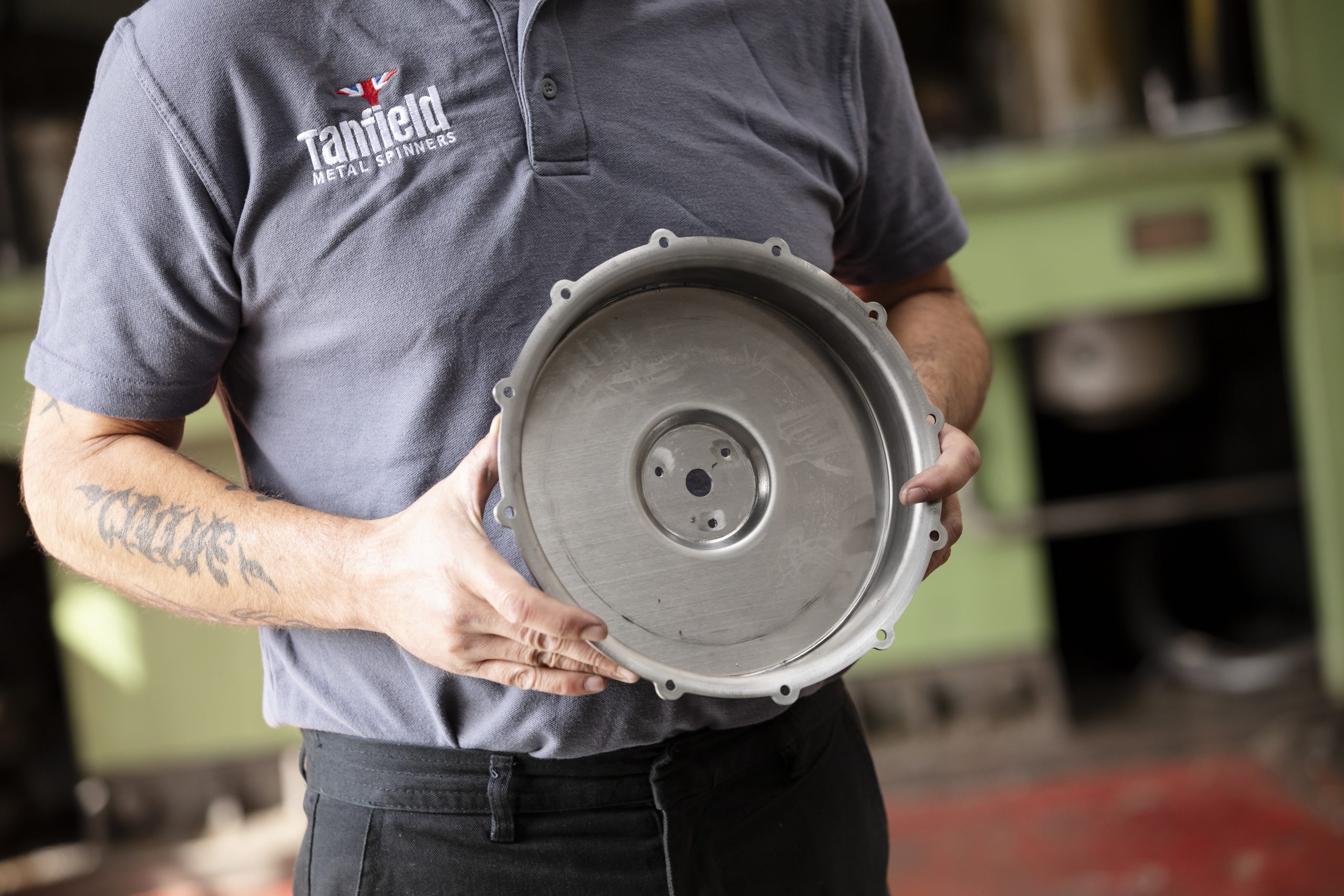
The Craft Behind the Process
While we can describe the metal spinning process in a linear manner, the reality is that each component requires a delicate balance of force, timing, temperature, and expertise. This balance of art and science is why the process ideally combines traditional craftsmanship with modern machinery—especially when working to tight tolerances or with exotic materials.
Whether delivering a prototype or part of an entire production run, custom metal spinning is a highly efficient and cost-effective way to manufacture symmetrical, hollow metal parts with seamless structure and high strength.
Partnering with Tanfield Metal Spinners
At Tanfield Metal Spinners, we’ve built our reputation on mastering every step of the spinning process. Our production lines handle everything from forming to polishing, while our highly trained team brings hands-on expertise to every job. With one of the largest tooling libraries in the UK, we can respond faster, spin more efficiently, and deliver precision-engineered results across countless industries.
Whether you need a one-off prototype or scalable production, we’re ready to help. Contact us today to discover how our spinning expertise can shape your next project.
Contact Us Today!
We encourage you to reach out to us today, our team of knowledgeable experts is ready to answer your questions, provide personalised guidance, and help you find the right solution for your needs.
Contact Us